نمودار پخت
نمودار پخت ارتباط بين زمان و تغييرات درجه حرارت در هنگام پخت مي باشد عوامل مؤثر در آن:
1-خروج آب خلل و فرج و آب پيوندي
2-سوختن و خروج مواد آلي و كربن موجود در بدنه
3-تجزيه و سوختن و خروج نا خالصي هاي گوگرد
4-اكسيداسيون و احياي اجزاي بدنه
5-تغييرات آرام حجمي
6-تبديلات ناگهاني و شديد حجمي ناشي از تبديلات پلي مورفيك
7-حداكثر درجه حرارت مناسب براي پخت بدنه
8-ابعاد ذرات
9- نفوذ پذيري و امكان عبور گازها از بدنه
نمودار پخت ارتباط بين زمان و تغييرات درجه حرارت در هنگام پخت مي باشد عوامل مؤثر در آن:
1-خروج آب خلل و فرج و آب پيوندي
2-سوختن و خروج مواد آلي و كربن موجود در بدنه
3-تجزيه و سوختن و خروج نا خالصي هاي گوگرد
4-اكسيداسيون و احياي اجزاي بدنه
5-تغييرات آرام حجمي
6-تبديلات ناگهاني و شديد حجمي ناشي از تبديلات پلي مورفيك
7-حداكثر درجه حرارت مناسب براي پخت بدنه
8-ابعاد ذرات
9- نفوذ پذيري و امكان عبور گازها از بدنه
تهيه منو پروسا
براي تهيه يك بدنه منوپروساي خوب نكاتي كه رعايت می کنیم كه عبارتند از:
– تركيب بدنه حتي الامكان بايد داراي كربنات حداقل باشد.
– تركيب لعاب، دمايی
– رژيم پخت
– اختلاف دما بين زير و روي رولر
– اعمال انگوب
– اساسي ترين نكته اي كه در انتخاب رژيم پخت مناسب بايد لحاظ شود، دماي تجزيه كربناتها حدود 940-930 درجه است و بايستي حتما مدتي بدنه را دراين دما نگه داريم اين دما براي كربنات منيزيم هم مناسب است چرا كه در 870درجه تجزيه مي شود لذا 4/1 كل سيكل پخت را به اين دما اختصاص مي دهند تا تكميل تجزيه كربنات كلسيم انجام پزيرد.
– نقطه نرم شوندگي اغلب لعابها، با دماي پخت حدود 1100درجه، نزديكي 550-500 است اما لعابهاي منوپروسا طوري طراحي شده اند كه نقطه نرم شوندگي آنها در حدود 700درجه است.
– هر چه نقطه نرم شوندگي لعاب بالاتر باشد، دماي لعاب بالاتر خواهد بود.
رژيم پخت:
– دماي ورودي كوره حدود 300درجه است.
– از دماي 600-300درجه ظرف مدت 7دقيقه دما افزايش مي يابد.
– از دماي 600 تا 930درجه ظرف مدت 2 دقيقه افزايش مي يابد.
– در دماي 1100درجه بين 5-3 دقيقه آنرا نگه مي دارند.
– از دماي 1100الي 850درجه تقليل ناگهاني دما را ظرف مدت 5دقيقه جهت پيشگيري از مات شدت سطح لعاب كوره انجام مي شود.
– از دماي 850درجه تا خروجي كوره ظرف مدت 10 دقيقه دما را كاهش مي دهند. كل اين سيكل 45 دقيقه است كه s.t آن 5 دقيقه و S.T آن 1100درجه است.
گفتني است دماي هنگام خارج شدن از كوره حدود 300 درجه است. 11 دقيقه از 45 دقيقه در دماي 930درجه است.
از دماي 400الي 900 درجه دما را سريعاً افرايش مي دهيم. آيا استحاله هاي پلي مرفيك سيليس سبب بروز مشكل نخواهد شد؟
در بدنه هاي منوپروسا كوارتز زيادي وارد نمي كنيم همچنين چون بدنه ها متخلخل هستند شوك پذيري بدنه افزايش لذا استحاله هاي كوارتز كمتر موثر خواهد بود.
اختلاف دما زير و روي رولر
در مرحله پيش پخت قبل از رسيدن به جهنم، دماي زير رولرها را بالاتر از روي رولرها انتخاب مي كنند. اين اختلاف بسيار بيش از اختلاف دمايي است كه در كاشي هاي كف انتخاب مي شود(در سيستنم تك پخت سريع) و گاهاً به 200درجه مي رسد.
مي دانيد كه انتقال حرارت در دماهاي بالا وبخصوص دماهاي بالاتر از 800 درجه بيشتر از طريق تشعشع صورت مي گيرد. وقتي دماي زير رولرها را بالاتر انتخاب مي كنيم حرارت بيشتري زير كاشي تشعشع مي كند در نتيجه با توجه به كمبود حرارت روي كاشي كه لعابدار است، دماي بدنه بيشتر از دماي لعاب خواهد بود لذا اين تدبير منجر به آن مي شود كه قبل از داغتر شدن لعاب و ذوب شدن آن تجزيه اجزاء فرار بدنه تشكيل شود.
اعمال انگوب:
اصولاً به سه دليل عمده انگوب اعمال مي شود
1- پوشاندن رنگ بدنه
2- تطابق بيشتر ضريب انبساط حرارتي بدنه و لعاب
3- كاهش احتمال بروز عيبpinhole
منظور ما در اينجا از اعمال انگوب، كمتر موارد 1 و 2 مي باشد و دليل عمده اعمال انگوب كاهش احتمال بروز عيبpinhole است.
تذكر:
هر چه وزن ليتر دوغاب بالاتر باشد يعني ميزان درصد آب دوغاب كمتر انتخاب شود ميزان تخلخلهاي موجود در قشر لعاب پس از خشك شدن كمتر خواهد بود.
تخلخلهاي موجود در قشر لعاب بعداً تبديل به حباب داخل قشر مذاب لعاب در حين پخت خواهد شد و بعداً اين حبابها مي توانند بهpinhole تبديل شوند.
در بدنه هاي منوپروسا اولين مشكل بروز عيبpinhole است. هنگاميكه وزن ليتر دوغاب بالاتر باشد و ويسكوزيته لعاب افزايش يافته و دوغاب تيكسوتروپ مي شود- نحوه اعمال دوغاب لعاب- چون خواهاهن يك لعاب كاملاً صاف هستيم روش اعمال آن بل ديسك نيست بلكه شيوه اي مي باشد كه اگر ويسكوزيته زياد باشد لعاب مواج مي شود لذا بايستي رس را كم و T.P.P بهآن بيفزائيم.
كم كردن ميزان رس از 8درصد به 5درصد و ميزان T.P.P حدودا%5/0 اضافه مي شود. با افزايش وزن ليتر احتمال دارد ضخامت لعاب بر بدنه ضخيم و كلفت شود براي جلوگيري از اين امرسرعت نوار نقاله را زياد مي كنيم
پینهول
مقوله پين هول در كاشي سالهاست كه از نقطه نظرات مختلف مورد بحث قرار گرفته و نتايج مفيد و موثري نيز در خصوص ماهيت و نحوه ايجاد آن بخصوص در بخش لعاب بدست آمده است. در اين مقاله بررسي هاي عملي در خصوص عوامل موثر در بروز پينهول از نقطه نظر اثرات بدنه كاشي و نيز شرايط فرايند توليد كاشي مورد بحث قرار گرفته است.
روش تحقيق و نتايج
1- اثر تك خاكها بر روي پين هول لعاب:
براي بررسي اين اثر تعدادي بيسكوئيت 5*10 سانتي متر را با پرس آزمايشگاهي از خاكهاي مصرفي در توليد بدنه و نيز خاكهاي مشابه تهيه گرديد و پس از پخت در كوره بيسكوئيت و اعمال لعاب؛ در كوره لعاب خط توليد پخت گرديد.نتايج نشان ميدهد كه خاكهاي آباده بيشترين تاثير را در پينهول لعاب بعد از پخت دارا مي باشد. لازم به ياداوري مي باشد كه هرچند در خاكهاي آباده نمكهاي محلول از نوع سولفاتها وجود دارد ولي نتايج آزمايشات بعدي نشان ميدهد كه عامل ايجاد پينهول در خاكهاي آباده عمدتاً ناشي از نمكهاي محلول نمي باشد، بلكه وجود مواد آلي در اين گونه خاكها يكي از عوامل موثر در ايجاد پينهول مي باشد. منحني D.T.A اين خاك بيانگر وجود مقدار زيادي مواد آلي مي باشد. از طرفي وجو مقدار زيادي پيريت در اين خاكها در كنار مواد آلي مي تواند نقش موثري را در ايجاد پين هول ايفا نمايد بويژه اگر منحني و اتمسفر پخت بيسكوئيت متناسب با ماهيت اينگونه خاكها نباشد. ولي با وجود اين باي بررسي نقش نمكهاي محلول در ايجاد پينهول آزمايشات زير صورت گرفت.
2- جدا كردن نمكهاي نا محلول از خاكهاي مصرفي:
در آزمايشي كه به همين منظور ترتيب داده شد با افزودن مقاديري كربنات باريم بيش از حد معمول(5%) به دوغاب بدنه شرايط رسوب سولفاتها فراهم آورده شد و پس از تهيه بدنه از دوغاب فوق، آن را در كوره پخته و سپس لعاب را بر روي آن اعمال نموده و در نهايت در كوره پخت داده شد. نتايج حاصله تغييرات مشخصي را در ميزان پينهول در مقايسه با نمونه هاي مرجع تهيه شده با همان شرايط (البته بدون استفاده از كربنات باريم ) نشان نداد.
در آزمايشي ديگر با استفاده از يك سمباده نرم سطح چند بيسكوئيت را سايش داده شد و لايه اي از روي آن برداشته شد و پس از تميز كردن سطح بيسكوئيت ها با پارچه هاي خشك و مرطوب، همراه با نمونه هاي مرجع آنها را لعاب داده و در كوره خط لعاب پخت داده شد. كاشي هاي مربوط به نمونه هاي سائيده شده داراي پينهول بيشتر و تا حدودي عميق تر نسبت به پينهول نمونه مرجع بودند كه اين مطلب به باقيماندن مقداري ذرات سائيده شده در روي بيسكوئيت قبل از اعمال لعاب نسبت داده شد ولي با اين حال در نمونه هاي ديگري كه كاملاً تميز و صيقلي شدهبودند نيز اين مشكل مشاهده مي شد.
در آزمايشي ديگر خاكهاي پينهول زا را جهت جداشدن نمكهاي محلول از آنها، ابتدا بطور مجزا در آب شسته شد و پس از جدا كردن آب جمع شده بر روي آنها، جهت تهيه بدنه مورد استفاده قرار گرفتند. اين آزمايش بر روي خاكهاي آباده انجام گرفت. شستشوي خاك همراه با آب فراوان در جارميل آزمايشگاهي صورت پذيرفت. آناليز آب جدا شده پس از شستشو نشان داد كه ميزان يون سديم از 23 به 29 و يون پتاسيم از 3/91 به 7/8 (p.p.m) افزايش يافته است. افزايش يونهاي فوق در آب جدا شده بيانگر وجود مقداري نمك محلول در خاكهاي مصرفي مي باشد. ولي بر اساس بررسي هاي بعمل آمده بر روي سطح لعاب خورده در اين بدنه ها مشخص شد كه تفاوت عمده اي از نقطه نظر ميزان پينهول بين نمونه هاي تهيه گرديده با خاكهاي شستشو داده شده و نمونه مرع نمي باشد لذا اين آزمايشات نشان داد كه نمكهاي محلول در خاكهاي مصرفي در افزايش پينهول نقش عمده اي ندارد.
3- بررسي اثر كائولن هاي مختلف جهت مصرف در لعاب بر روي پينهول:
جهت بررسي اين مورد كائولن هاي متفاوتي بر روي يك فريت مرجع آزمايش گرديد (با فرمول تركيبي 7% كائولن و 93% فريت اپك 84-21-120 لعابيران) و مطابق شكل 3 كائولن هاي مختلف بر حسب ميزان پينهول منتجه در لعاب، دسته بندي گرديدند.
همانگونه كه در شكل نشان داده شده است كائولن زدليتز كمترين ميزان پينهول را در لعاب ايجاد مي نمايد. براي بررسي علل اين مسئله سعي بر آن شد تا عوامل مولد پينهول در يكي ديگر از كائولن هاي مصرفي كارخانه (W.B.B) مورد بررسي قرار گيرد تا از اين طريق بتوان به علت تفاوت نقش كائولن ها در ايجاد پينهول پي برد. با بررسي هاي اوليه مشخص گرديد كه تركيب W.B.B با زدليتز بخصوص از نقطه نظر كانيهاي موجود و ناخالصي ها متفاوت است. بخصوص درصد ميكاي كائولن W.B.B بيشتر مي باشد. براي بررسي بيشتر آزمايشات زير صورت گرفت:
4- بررسي اثر ناخالصي هاي كائولن W.B.B:
جهت بررسي دقيق تر كائولن W.B.B (كائولن مصرفي كارخانه) آزمايشاتي بر روي اين كائولن انجام گرفت.
اين آزمايشات شامل: 1- تلاش در جهت كاهش ميكاي موجود در كائولن. 2- جداكردن ناخالصي هاي موجود در كائولن مي باشد. جهت جدا كردن ميكا روشهاي مختلفي تست گرديد كه موثرترين روش استفاده از ريز ترين الك موجود و عبور دادن كائولن از اين توري بود (توريT100) در اين حالت دانه هاي بسيار ريز و ورقه اي و درخشان ميكا به همراه انواع ناخالصي هاي ديگر بر روي توري باقي مي ماند. منحني D.T.A از اين مواد نشانگر از وجود مقادير زيادي مواد آلي در بين ناخالصي ها بود كه خود ميتوانست تا حدودي منشا پينهول باشد اين مسئله با جمع آوري مقدار زيادي از اين ناخالصي ها (حدود 2 گرم) بوسيله عبوردادن چند كيلو گرم كائولن W.B.B از توري و استفاده از آن در لعاب تائيد گرديد.
علاوه بر آن به منظور تحقيق از اثر مخرب ميكا در لعاب آزمايش ديگري ترتيب داده شد كه نتايج آن در شكل 4 آورده شده است. بايست توجه داشت كه اندازه دانه هاي ميكاي مصرفي در اين آزمايشات در مقايسه با ميكاي جداشده از كائولن W.B.B بزرگتر بود و لذا به شدت در ميزان پينهول تاثير گذاشته بود.
5- اثر ضخامت لعاب اعمالي بر روي ميزان پينهول:
در اين آزمايش وزن هاي مختلفي از لعاب بر روي چندين بيسكوئيت بر روي خطوط لعاب توليد اعمال گرديد. همانطور كه در شكل 5 آورده شده نشان ميدهد كه كاهش ضخامت لعاب باعث افزايش ميزان پينهول مي گردد.
6- اثر زمان نگهداري دوغاب:
آزمايشات مربوط به فاكتور فوق در چند مرحله انجام پذيرفت. در مرحله اول اين آزمايشات در خط توليد و با استفاده از يك همزن كنار خط لعاب صورت گرفت ولي بدليل شرايط تاثيرگذار در نتيجه آزمايشات و متاثر شدن ميزان پينهول از عواملي نظير شرايط مختلف پخت در روزهاي متفاوت و استفاده از بيسكوئيت هاي توليدي مربوط به روزهاي مختلف و نيز شرايط باند در طول مدت 9 روز انجام آزمايشات نتيجه گيري مفيدي حاصل نشد.
در سري آزمايشات بعدي بطور دقيق تر جزئيات وضعيت دوغاب و تغيير آن در اثر گذشت زمان بررسي گرديد. براي اين منظور بطور متوالي طي 15 روز تغييرات PH و نيز ميزان يونهاي Ca,Na,K موجود در دوغاب يك لعاب مرجع اندازه گيري و تعيين گرديد. نتايج حاصله به اين نكته اشاره دارد كه ميزان يونهاي Na,Kبا گذشت زمان تغيير زيادي نمي كند، اما ميزان يون Ca در دوغاب لعاب با افزايش زمان بيشتر مي شود و در همين راستا PH را نيز تحت تاثير قرار مي دهد. از طرفي يكسري آزمايشات ديگر نشان داد كه با باز بودن درب حوضچه هاي موجود در كنار خطوط لعاب باعث تشديد اين وضعيت شده چرا كه با تبخير آب ميزان نمكهاي موجود در آب افزايش مي يابد.
همانگونه كه در ابتدا گفته شد در برخي از خاكها ي مصرفي كارخانه مقادير زيادي مواد آلي به همراه پيريت مي باشد. براي خروج اينگونه مواد و همچنين تجزيه و اكسيداسيون پيريت دو عامل مهم يعني زمان و اتمسفر اكسيدي نقش بسيار مهمي را ايفا مي كنند. براي بررسي نقش اين دو فاكتور آزمايشات شماره 8 و 8 انجام گرديد.
7- بررسي اثر نمودار پخت بيسكوئيت در ميزان پينهول لعاب:
در بررسي انجام شده بر روي تاثير شرايط پخت بسكوئيت و لعاب بر ميزان پينهول آزمايشاتي جهت بررسي شرايط پخت بيسكوئيت و اثر آن بر پين هول ترتيب داده شد. به اين منظور نمودار پخت، مربوط به كوره هاي تونلي پخت بيسكوئيت خط توليد، طي محاسباتي در كوره الكتريكي قابل برنامه ريزي آزمايشگاه شبيه سازي گرديد. نتايج آزمايشات همانطور كه در شكل 6 مشخص شده است نشان ميدهد كه بيسكوئيتهاي پخته شده در كوره الكتريكي در مقايسه با بيسكوئيت هاي پخته شده در كوره هاي بيسكوئيت خط توليد (بيسكوئيت ها همگي مربوط به توليد يك پرس) با همان نمودار پخت، پس از اعمال و پخت لعاب داراي پينهول كمتري بود كه نشان از تاثير شرايط محيطي پخت در خط توليد دارد. علاوه بر آن در آزمايشات بعدي ضمن تغيير نمودار پخت عادي در كوره الكتريكي، ميزان زمان توقف بيسكوئيت ها در دو محدوده دمائي (600-400) و (900-750) درجه سانتيگراد به دو برابر مدت زمان معمولي افزايش داده شد و نتايج نشان داد كه نمونه هاي پخته شده در اين شرايط در مقايسه با نمونه هاي پخته شده در شرايط عادي (هر دو سري در كوره الكتريكي) پس از اعمال لعاب و پخت داراي پينهول كمتري بودند (شكلهاي 6A,6B)اين خود نشان از عدم كارايي مناسب منطقه پيش پخت در كوره توليد مي باشد.
همانگونه كه گفته شد افزايش زمان در منطقه پيش پخت ميتواند فرصت كافي را براي اكسيداسيون مواد آلي و تجزيه پيريت و خروج به موقع گازها فراهم سازد كه اين امر خود در كاهش پينهول نقش مهمي دارد.
حال به بررسي اجمالي كوره هاي رولري مي پردازيم
A : ساختار
كوره رولر داراي يك ساختار فولادي است كه تكيه گاه كف ، ديواره ها وسقف آن از مواد مختلفي مانند مواد ديرگداز ، عايق و سراميك ساخته شده اند كه با ابعاد ، ميزان عايق بودن و مقاومت بالا در مقابل شوك هاي حرارتي توصيف مي شود. تمامي اين مشخصات اجراي نمودار پخت و سرعت گرم شدن وسرد شدن كوره را تسهيل مي كند.
B: سيستم محرك وگرداننده رولر
حمل بدنه كاشي ها در كوره توسط مجموعه اي از موتور و رولر ها صورت مي پذيرد كه جنس لوله ها در بعضي قسمت ها فولادي و در بعضي قسمت ها سراميكي است و ويژه گي آنها براي تمامي دما هاي پيش بيني شده مناسب است.
اين سيستم داراي قسمت هاي مجزايي است كه به موتور هاي مستقلي كه سرعت آنها به صورت مستقل قابل تنظيم است مجهز ميباشد و اين سيستم بهره برداري بهينه از منحني پخت را امكان پذير ميسازد و به ما امكان مي دهد هرگاه احتمال برخورد كاشي ها به هم وجود داشته باشد ميتوان بين رديف ها فاصله ايجاد كرد و باعث حركت منظم كاشي ها شد. براي انجام دقيق اين عمل سرعت قابل تنظيم موتور توسط كامپيوتر كوره كنترل مي شود.
C : سيستم احتراق
اين قسمت شامل مشعل هايي است كه با گاز (يا نفت سفيد و گازوييل ) و دمش هوا كار ميكند . اين مشعل ها به صورت دسته هاي مستقل با وسايل كنترلي اتوماتيك و دستي در قسمت بالا و زير رولر ها قرار دارند . در تنظيم هر چه بهتر اين مشعل ها كنترل فشار هوا (با منومتر ) اهميت زيادي دارد همانند سيستم محرك و گرداننده رولر كنترل دماي حاصل از مشعل ها با كامپيوتر انجام مي شود.
D : بخش هاي مختلف كوره
كوره به شش بخش تقسيم مي شود .
1 – پيش كوره (per kiln )
اين بخش توسط مواد سراميكي عايق شده و براي دماهاي پايين (200 تا 400) مناسب است . اين قسمت مشعل ندارد و بوسيله ساكشن هواي گرم كه توسط فن هاي مكنده از قسمت هاي بعدي به اين قسمت منتقل مي شود گرم ميگردد. اين مكنده ها در ابتدا و انتها و بالا و زير رولر هاي پيش كوره هستند. نقش اصلي اين بخش حذف كامل رطوبت پس از دراير و يا لعاب زدن است . اين عمل به منظور جلوگيري از شكستن و ترك خوردن كاشي در حال پخت در اثر تبخير بسيار شديد آب در بخش بعدي ميباشد.
2 – پيش گرم (per heating)
اين بخش داراي نوعي عايق با دماي نسبتاً بالاست به همين دليل از مواد دير گداز و مقاوم در برابر حرارت و قطعات سراميكي استفاده شده است . با توجه به منحني هاي پخت اين بخش تا حدود 900 درجه گرم ميشود و در اين بخش دما طوري تنظيم مي شود كه آب تركيبي آزاد شده ، كوارتز تغيير شكل دهد ، احتراق مواد آلي به صورت كامل صورت پذيرد و كربنات ها تجزيه شوند. در اين بخش ماشين آلات احتراق طوري ساخته شده اند كه بتوان تغييرات را در گستره وسيعي انجام داد .
3 – پخت (firing )
اين بخش از دمايي شروع مي شود كه كه حدود 900 درجه است (بسته به نوع كاشي تا 1200درجه ) و عايق مربوط به خود را دارد. در اين بخش براي كنترل دقيق تر مشعل ها آنها را به دسته هاي كوچكتر تقسيم ميكنند تا اعمال نمودار پخت كه در اين ناحيه پيچيده تر است ممكن شود. اگر دماي اين بخش درست تنظيم نشود با مشكلاتي مانند مسطح نبودن ، ناهموار بودن ، ناهماهنگي ابعاد ويكدست نبودن ميزان شيشه اي شدن لعاب مواجه خواهيم بود.
4 – سريع سرد كردن (rapid cooling )
دما در اين ناحيه بين دماي پخت تا تقريبا 600 درجه را شامل مي شود . هوا در اين قسمت توسط مجموعه اي تنظيم مي شود كه شامل يك servomotor با شير پروانه اي خود كنترل است كه توسط ترموكوپل هاي موجود در كوره تنظيم مي شود .
5 – خنك كردن عادي (natural cooling )
اين ناحيه نيز با توجه به اينكه دما در آن از حدود 600 به 500 كاهش مي يابد از حساسيت زيادي برخوردار است و بايد شيب كاهش دما در اين بخش ملايم باشد چون بايد فرآيند تغيير شكل كوارتز بدون ترك خوردن بدنه رخ دهد.
6 – سرد شدن نهايي ( final cooling )
دما در اين ناحيه زير 500 درجه است . در اين بخش هوا ي محيط به قسمت بالا و پايين بدنه ميدمد تا دماي آن در خروجي به زير 100 درجه برسد .
عيوب:
تقريباً كليه عيوب پس از پخت نمايان مي گردد. اما فقط تعدادي از آنها مربوط به كوره هستند البته طبقه بندي عيوب بر اساس منشا آن كار سختي است چون علت ايجاد يك عيب ممكن است يك عامل نباشد. اما ميتوان عيوب اصلي كه در هر فرآيند مشخص مي شود را با ديگر فرآيند ها مورد مقايسه قرار داد .
1 – ترك هاي پيش گرم
به صورت شكستگي هاي نا برابر از لبه به سمت مركز وجود دارند .
– طول آنها 3 تا 4 سانتيمتر است.
– تعداد آنها هميشه بيش از يكي است.
– دليل آن بالا بودن دماي منطقه پيش گرم است .
2 -مغز سياه (black core ) :
در اثر احتراق ناقص مواد آلي در داخل بدنه مشاهده مي شود .
– در بدنه هاي سفيد به رنگ هاي زرد – سبز و خاكستري ديده ميشود.
– در بدنه هاي قرمز به رنگ هاي زرد – سياه و خاكستري ديده ميشود.
اين عيب ممكن است باعت تغيير شكل و اندازه كاشي شود و سوراخها و ترك هايي در لعاب پديد آورد و در لعاب ايجاد سايه نمايد .
به طور كلي همه عواملي كه باعث جلوگيري از خروج گاز ها از بدنه ميشوند ، مانند رطوبت ، دانه بندي ، فشار پرس ، ضخامت زياد نقطه ذوب لعاب و بدنه باعث ايجاد اين عيب شوند .
براي رفع اين عيب بايد كاشي در دماي پيش گرم كه قبلاً به آن اشاره شد بيشتر بماند تا احتراق مواد آلي كامل گردد . در اثر عيب مغز سياه سه وضعيت به شكل هاي زير متصور است.
دليل : اگر وجود عيب در يك طرف كاشي باشد نشان از مشكل در پر كردن قالب در حين پرس است كه بيانگر عدم كنترل تراكم (penetrometer) در نقاط مختلف كاشي در پرس است و اگر عيب در تمامي پيرامون كاشي باشد بيان مي كند كه سرعت ضربه پرس بالا بوده است.
دليل : فشار پرس بالاست يا اينكه لعاب در دماي پايين تر ذوب شده و مانع از خروج گاز ها از بدنه شده است و احتراق ناقص مانده . كه بايد مقداري هوا از قسمت روي كاشي به لعاب داده شود تا دير تر ذوب گردد.
دليل : وجود ناخالصي ويا وجود لخته هاي رطوبتي پودر در بدنه باعث چنين عيبي مي شود اين عيب در كوره حل نمي شود و بايد الك هاي پرس و ماشين آلات آن قسمت مورد بازديد قرار گيرد .
3 – عيوب شكل هندسي
طي فرآيند پخت بدليل عدم تنظيم مناسب مراحل مختلف ممكن است كاشي ها دچار دفرمگي با اشكال مختلف هندسي شوند كه توضيح هر تعدادي از عيوب با شكل در زير مي آيد.
شكل 1
با شرط اينكه فراواني عيب در همه محل ها يكسان باشد و در واحد زمان خيلي تغيير نكند ،هر گاه كاشي به ميزان بالاي شيشه اي شدن برسد اين مشكل مشاهده مي شود كه بايد روي پارامتر هاي زير كار شود.
1- اندازه ذرات پودر(كنترل مش )
2- دانسيته قسمت هاي پرس شده – رطوبت و فشار پرس
3- گرما در قسمت پيش گرم
4- شيب حرارتي در نواحي بحراني
با شرط اينكه فراواني عيب در همه محل ها يكسان باشد و در واحد زمان خيلي تغيير نكند ،اين عيب در قطعات كناري كوره كمتر مشاهده مي گردد و مربوط به ناحيه پخت است .
براي رفع اين مشكل با در نظر گرفتن سايز متوسط به صورت زير عمل مي كنيم.
1- اگر ابعاد صحيح بود دما در قسمت بالاي سطح رولرها را (5 تا 10 درجه يا كمي بيشتر) كاهش داده و در قسمت پايين زياد مي كنيم .
2- اگر ابعاد بزرگتر بود دما را 5 تا 10 درجه و يا كمي بيشتر در زير سطح رولر ها افزايش مي دهيم .
3- اگر ابعاد كوچكتر بود دما را به ميزان 5 تا 10 درجه در بالاي سطح رولر ها كاهش مي دهيم .
با شرط اينكه فراواني عيب در همه محل ها يكسان باشد و در واحد زمان خيلي تغيير نكند ، نشان ميدهد دما در قسمت بالا و زير سطح رولر ها يكسان نيست پس با توجه به سايز متوسط ابعاد كاشي هاي خروجي از كوره تنظيم هاي زير را انجام مي دهيم .
1- اگر ابعاد صحيح بود دما را درپايين 5 تا 10درجه كاهش و به همان اندازه در بالا افزايش مي دهيم.
2- اگر ابعاد بزرگتر بود دما را 5 تا 10درجه و ياكمي بيشتر در بالاي سطح رولر ها افزايش مي دهيم.
3- اگر ابعاد كوچكتر بود دما را به ميزان 5 تا 10 درجه در زير سطح رولر ها كاهش مي دهيم.
با شرط اينكه فراواني عيب درهمه محل ها يكسان باشد و در واحد زمان خيلي تغيير نكند ،نشان ميدهد دما در قسمت بالا و زير سطح رولر ها يكسان نيست پس با توجه به سايز متوسط ابعاد كاشي هاي خروجي از كوره ، تنظيم هاي زير را انجام مي دهيم .
1- اگر ابعاد صحيح بود دما را در بالا 5 تا 10 درجه كاهش و به همان اندازه در پايين كاهش مي دهيم
2- اگر ابعاد بزرگتر بود دما را 5 تا 10درجه و يا كمي بيشتر در زير سطح رولر ها افزايش مي دهيم
3- اگر ابعاد كوچكتر بود دما را به ميزان 5 تا 10 درجه در بالاي سطح رولر ها كاهش مي دهيم
با شرط اينكه فراواني عيب در همه محل ها يكسان باشد و در واحد زمان خيلي تغيير نكند ، بخشي از كوره در مورد اين شكل اهميت دارد كه دما در آنجا 800 تا 900 درجه و50 تا 100 درجه است .
بايد دماي بالاي سطح رولر ها را افزايش و پايين را كاهش داد .
با شرط اينكه فراواني عيب درهمه محل ها يكسان باشد و در واحد زمان خيلي تغيير نكند اين عيب ممكن است مربوط باشد به :
1- كاشي در ناحيه سريع سرد شدن (rapid cooling ) كه در رديف هاي دنبال هم قرار دارد به يكديگر فشار مي آورد . (سرعت را افزايش دهيم )
2- اين شكل حالت شديد تر شكل يك است (از راهكار مربوط استفاده كنيم ) بايد توجه داشت كه هميشه رد گيري كردن دماها به منظور توجيه اين پديده كفايت نمي كند مخصوصاً زماني كه اين پديده ها به دنبال توقفات كمابيش طولاني اتفاق مي افتد و همچنين كنترل فشار گاز و هوا براي مشعل ها را بايد مد نظر قرار داد.
اشكال زير معمولا داراي فراواني يكساني نيستند ولي به صورت پيوسته وجود دارند تغيير شكل اين عيوب بستگي زيادي به نحوه شارژ كوره دارد (فرستادن كاشي به داخل كوره ) از قبيل اينكه فاصله بين كاشي ها و خالي بودن رديف ها و تميز بودن رولر ها و…
بنا بر اين مشكل را ميتوان با انتخاب تمهيدات لازم براي اصلاح شكل هندسي شارژ و همچنين نگهداري دقيق رولر ها حل نمود و ناحيه بحراني براي اين عيوب بخش firing و rapid cooling است
باتوجه به مفاهیم اولیه و اصولی و منطقی گفته شده در این پروژه طبق تجربه شخصی لینک روش پخت در جدول فایل PDF پیوست شده که میتوانید آن را برسی کنید.
لازم ست قبل از اجرا روی بدنه های سفال و سرامیک یک بار تست کنید تا نتیجه مطلوب تری داشته باشید.
باآرزوی موفقیت برای شما مسعود صبوری
فایل PDF
لینک ویدو پرسش پاسخ در اینستاگرام…..
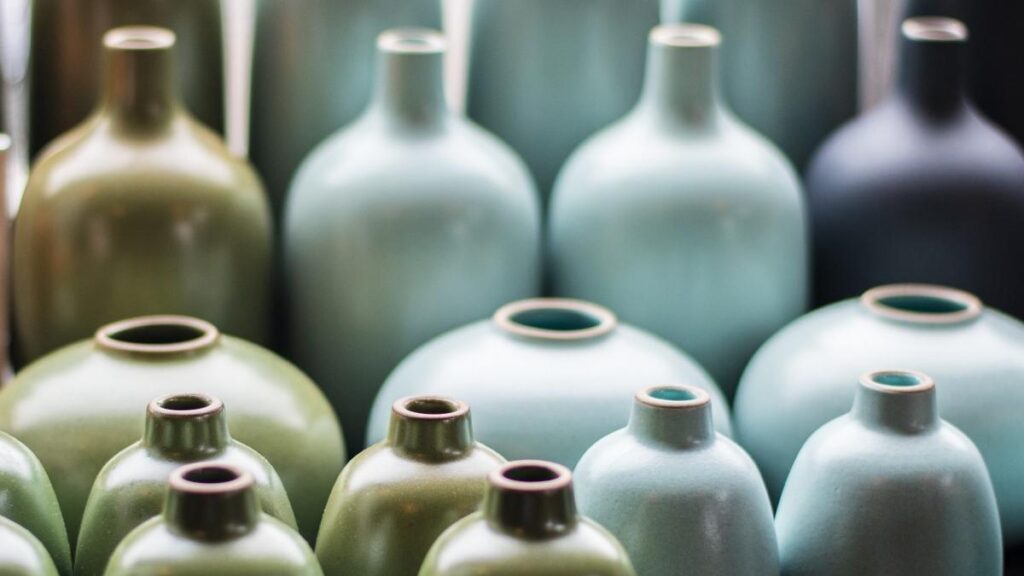